-
WhatsApp
-
Email
The rotary evaporator is an experimental instrument, which is used in chemical experiments in major universities and laboratories. Different experiments use different rotary evaporators, and the parts of the rotary evaporators used are also different. However, in general, the purpose of using a rotary evaporator is mostly the same, basically for distillation extraction, material crystallization and solvent separation. Therefore, the components of the rotary evaporator are basically the same,
Next, this article will introduce two parts in detail: Rotary evaporator parts and Rotary evaporator working principle
Next, this article will introduce two parts in detail: Rotary evaporator parts and Rotary evaporator working principle
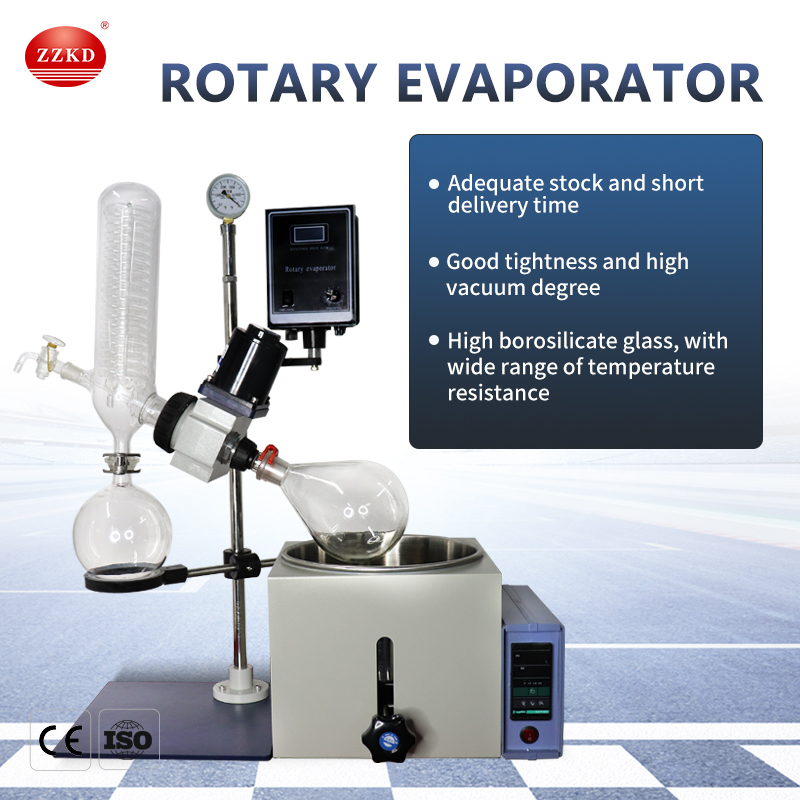
Rotary evaporator working principle:
The working principle of the rotary evaporator: First, the temperature of the rotating bottle is controlled by heating the water (oil) bath, so that the temperature in the water bath meets the requirements. The motor drives the rotating bottle to run at a preset speed. At the same speed, rotate at a constant speed to increase the evaporation area. The evaporating flask is under negative pressure by means of a vacuum pump. The evaporation flask is placed in a water bath for constant temperature heating while rotating, and the solution in the flask is heated, diffused and evaporated in the rotating flask under negative pressure. The rotary evaporator system can be sealed and decompressed to 400-600 mmHg; the solvent in the distillation flask is heated with a heating bath, and the heating temperature can be close to the boiling point of the solvent; at the same time, it can be rotated at a speed of 50-160 revolutions per minute, The solvent is formed into a thin film and the evaporation area is increased. In addition, it is processed by a decompression cooling unit composed of a vacuum acquisition device to efficiently separate or distill the material.This is how a rotary evaporator working principle
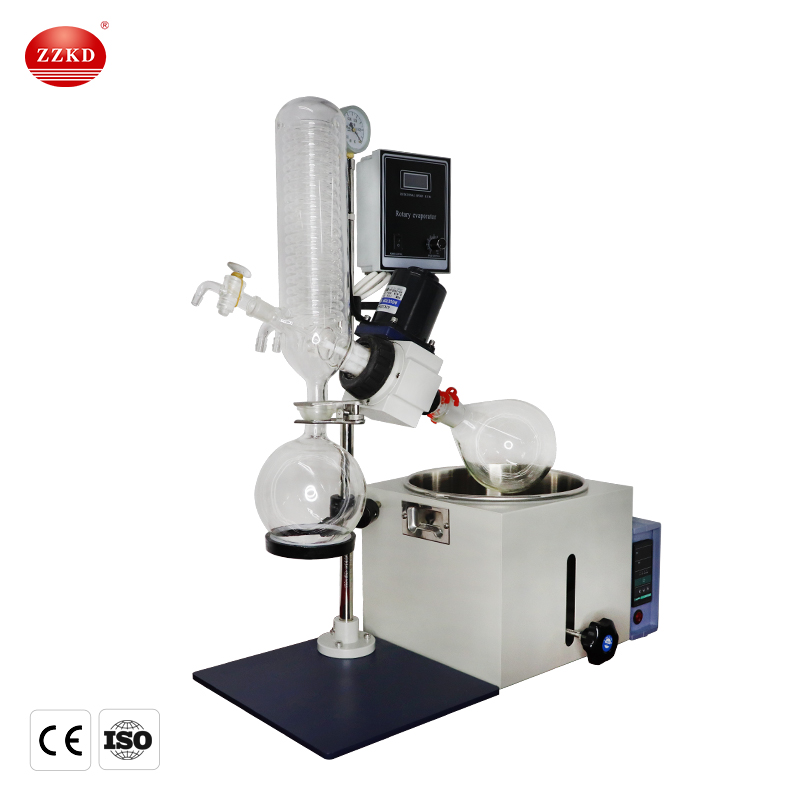
Rotary evaporator parts:
The rotary evaporator is mainly composed of four parts: the glass part, the water bath part, the sealing part, and the motor part.
First: Glass Components The glass part is mainly composed of condenser, rotating bottle, receiving bottle, cross bottle, feeding piston (with PTFE tube) and glass through shaft. The shape of the condenser is mostly double snake surround type. This structure can increase the heat exchange area and greatly improve the condensation efficiency of the material. The condenser has two interfaces: an external low temperature circulating liquid pipeline interface and a pressure reducing device interface. It can be adjusted according to demand to further improve the condensation efficiency. The general cooling medium of the condenser is water. If the ambient temperature is high and the condensation effect is not good, it can be replaced with ethanol. The material of the rotating flask is generally GG17 high borosilicate glass, and the shape is an eggplant-shaped or round-bottomed flask with a standard ground interface, which is connected to a decompression pump through a certain height reflux serpentine condenser. The rotary bottle is basically fixed, and the height of the oil bath is raised and lowered by the iron frame to adjust the contact between the oil bath and the rotary steamer. When feeding, it is different from directly pouring material into the rotary evaporator in the laboratory, and the material is sucked through the feeding valve. The materials contained are generally ½ or a little more than the capacity of the rotary bottle, so be sure to pay attention to the model when purchasing products. Small-capacity receiving bottle There is no discharge port below 3L, and there is a discharge port above 5L. The receiving bottle above 5L has an air outlet and a vacuum exhaust port, which is connected to the other opening of the reflux condenser to receive the evaporated organic solvent. With the four-way bottle structure, the concentrated liquid can be directly returned to the collection bottle from the condenser tube, and will not flow back into the sample bottle and will not contaminate the sample.Rotary evaporator parts: feed piston and glass through shaft, the diameter and length of which are also different for different experimental needs.Second: the components of the water bath
Second: the components of the water bath Rotary evaporator parts: water bath, The main function of the water bath is to heat the material and control the temperature of the water bath to reach the required temperature. The general heating medium is clear water, generally distilled water, so as to avoid scale formation in the pot. If there is a special requirement for temperature, it can be replaced with silicone oil or high temperature silicone oil. There will be a cover on the water bath pot, which is not used frequently during use, but it can effectively prevent dust from entering the water bath or oil bath during the static time, and keep the water bath or oil bath clean. At the same time, the following points need to be paid attention to: 1. The power of the water bath is different for different models. 2. The controller of the water bath can only control the temperature in the pot, but not the temperature in the bottle. The explosion-proof water bath is different from the ordinary water bath controller, and the explosion-proof type is one third smaller than the ordinary one. 3. Different Models have different lift heights. 4. There is no water in the water bath and cannot be energized
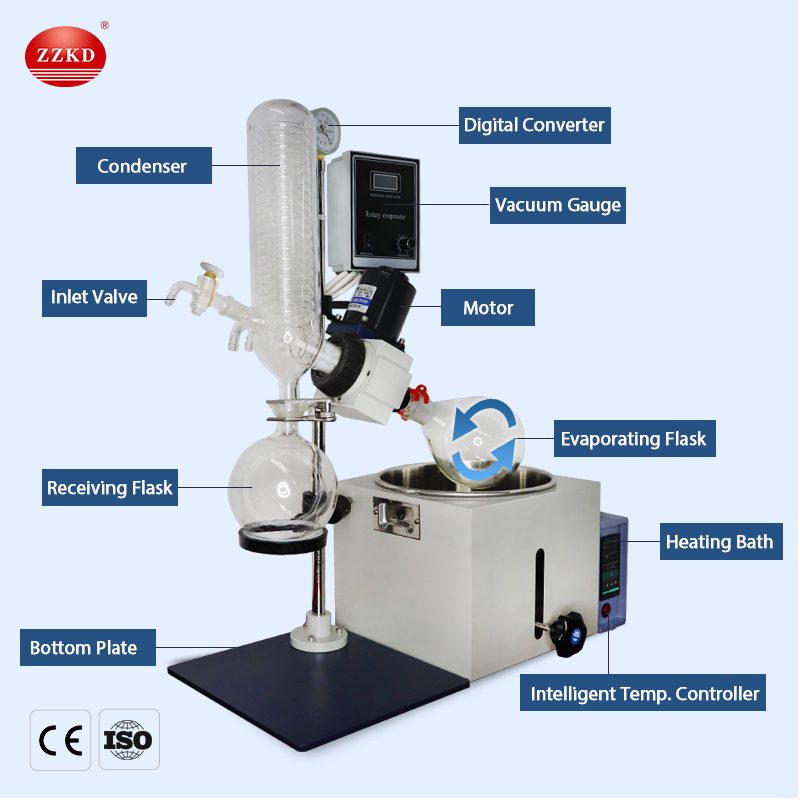
Third: sealing components The sealing part is mainly composed of sealing flanges. The principle is that as the gap between the flanges shrinks, the gasket is squeezed and deformed, and the gasket material fills the gap on the groove surface, thereby eliminating the medium leakage channel and achieving sealing. effect. Compared with rubber wood, the sealing flange is stronger and more resistant to high temperature and wear. The flange oil is composed of three parts, the black material is rubber wood, the white material is PTFE, and the light yellow material is nylon. Both the sealing interface and the sealing ring need to be coated with a layer of vacuum grease before installation. After the installation is completed, clamp the vacuum hose, observe the vacuum gauge, check whether the instrument maintains the vacuum, and at least observe to ensure that there is no air leakage for 5 minutes. If there is air leakage, check whether the sealing interface and sealing ring are installed properly.
Fourth: motor part Rotary evaporator parts:motor part. Motors are divided into rotating motors and lifting motors. The rotating motor is the main component of the rotating mechanism, which can be an AC motor or a DC motor. The operation of the rotary evaporator needs to be driven by electricity, and requires a uniform speed operation. The user can control the steady-state speed of the rotary flask through the control panel, so as to drive the distillation flask to rotate at a uniform speed. This rotation method is more suitable for various experimental requirements.