-
WhatsApp
-
Email
The sedimentation centrifuge is used for solid-liquid phase separation of solid suspensions with granular phases, and it can also be used for solid-liquid phase separation of fibrous materials. It is especially suitable for ethanol extraction of CBD oil. The whole body is made of stainless steel and meets GMP specifications for use in the food industry.
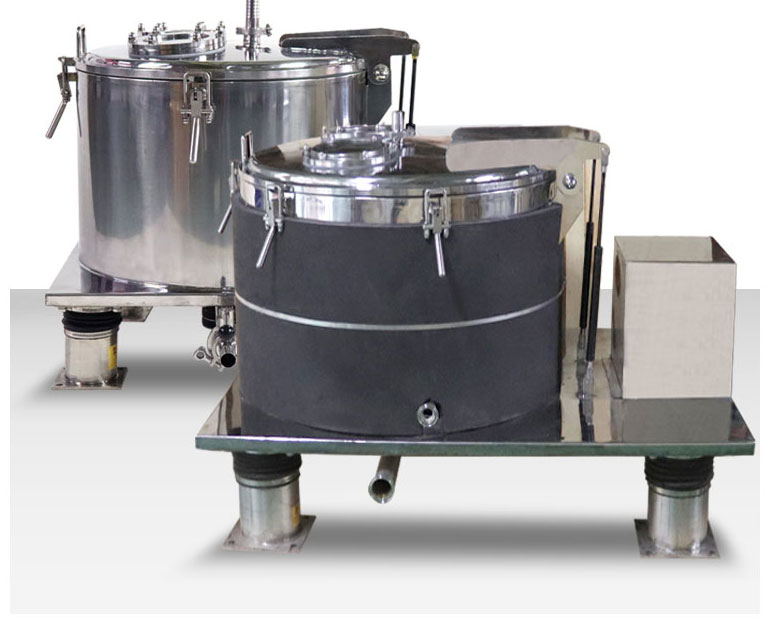
Overview of the process of extracting CBD using a centrifuge
Operator fills filter bag with milled plant material and places it into the machine.
Then flooded the centrifuge, and bi-directionally agitated for full target compound removal.
After washing, the plant material undergoes a high speed spin dry to remove the liquid as much as possible.
The alcohol wash is then collected to containers for further processing.
Centrifuge Introduction:
The PPTD centrifuge is top discharging, hermetic closure type equipment. The material is fed into the drum through the feeding pipe on the hermetic closure casing; under the action of the centrifuge force field, the liquid-phase passes through the filter medium and the discharged out of the machine, while the solid-phase material is retained inside the drum, after the machine is stopped, the material is discharged from the top. The centrifuge has such features as smooth running, easy & convenient operation as well as conducting feeding, washing and dehydrating under the state of hermetic closure, etc.
Features:
1.Plate type structure.
2.Four support, equipped with high viscosity elastic damping shock absorbers.
3.Variable frequency drive with PLC system and touch screen for auto/manual controls.
4 .Sanitary Stainless Steel Construction.
5.Bi-Directional Agitation.
6. Easy Material Loading/ Unloading.
7. Variable Speed Control
8. No foundation required.
9.Low temperrature with jackets for cooling circle liquid.
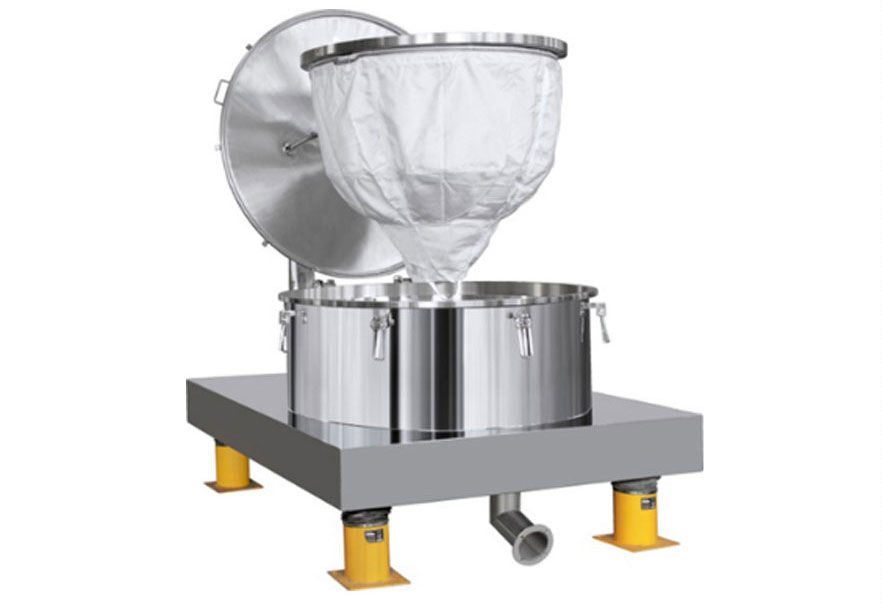
Main components of basket centrifuge
1.Ex-proof motor.
2.Frequency conversion control box.
3.PTFE Seals.
4.Filter bags.
5.Clamp joint for feed and drain port.
6.Sight hole with stalinite.
7.Power assisting device for opening/closing the lid.
8.SS304 lifting hook for hoisting the filter bag.
9.Valve for cooling circulating liquid and discharging soaking liquid.
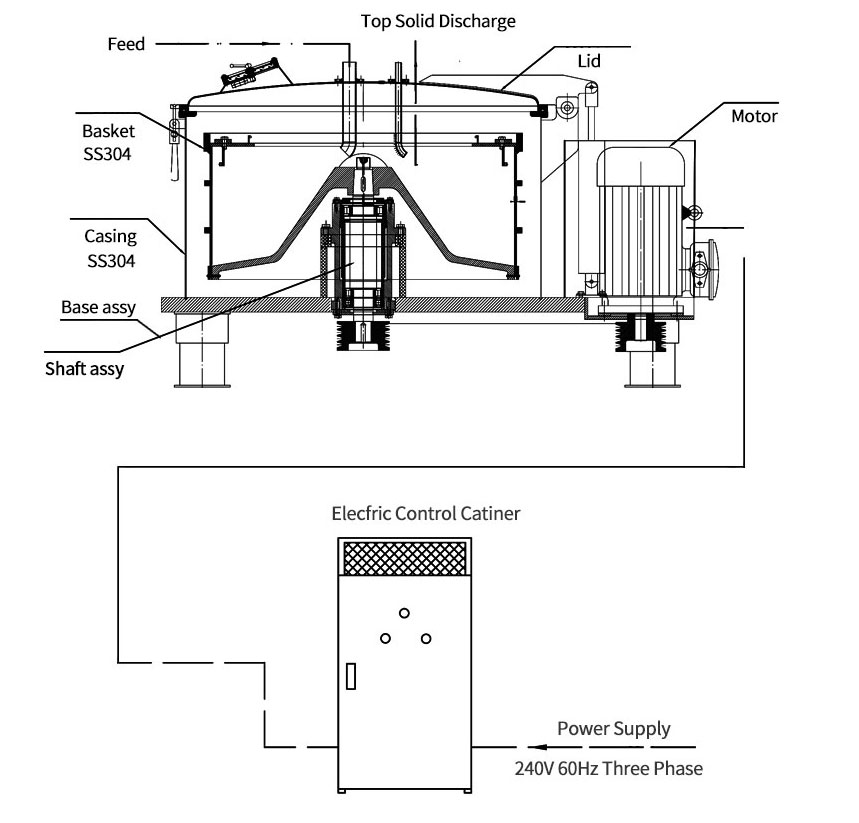
Design of main components of stainless steel centrifuge
Base parts:
● Flat structure. Q235A steel plate is used for welding and the surface is lined with 304 stainless steel plate. The machine has a low center of gravity and stable operation. Easy to install.
● The casing and the base (flat plate) are welded as a whole, and the rigidity is good.
● 4 liquid damping vibration isolator support systems are used under the base, which has good vibration damping performance. Minimize interference to surrounding equipment and foundation ground.
Drum parts:
● In the drum parts, the bottom of the drum is made of cast steel 304, and the material of the drum body 304 and the baffle plate 304, the bottom of the drum, and the liner are fully welded. The weld seams are smooth and the inner and outer surfaces are polished. The drum has undergone strict dynamic and static balance testing, which has good balance and 100% non-destructive inspection of the weld.
Bearing seat and main shaft:
● The inner and outer design of the bearing seat can be lifted vertically from the upper part for easy disassembly and maintenance, and the seal is reliable. The main shaft adopts 40Cr and has been quenched and tempered, the bearing has a long bearing length and good bearing performance. , The sealing effect is good, the stainless steel sleeve is placed on the low-continuity part of the main shaft and the drum to ensure the corrosion resistance of the main shaft; the bearing adopts high-quality bearings.
Housing components:
● The material contact part is made of 304 material, with a large flip cover structure, equipped with washing pipes, squint mirrors, explosion-proof lights, all fasteners are stainless steel; the inner and outer surfaces are polished.
● The cover is a large spring-type flip cover, and the seal adopts silicone rubber, which can realize the requirements of airtight and explosion-proof.
Material used in centrifuge
● The centrifuge shell is made of 304;
● The bottom of the drum is cast steel liner 304;
● All small parts on the cover are made of 304;
● The shaft seat of the centrifuge frame is made of Q235, and the part in contact with the material is lined with 304;
● 40Cr steel quenched and tempered;
● The remaining contact materials are made of 304.
Motor parts
● Motor parts adopt explosion-proof 18.5KW motor (explosion-proof grade EX.dIIBT4)
Control System
● The main motor uses a frequency converter to regulate the speed;
● The inverter and the production unit are jointly controlled, with high reliability and strong anti-interference ability;
● The brake is electrically braked by the inverter and the production unit, and is provided with motor overheating and overload protection.
![]() |
![]() |
![]() |
Working Steps:
● System loading: A pre-loaded closed filter bag is placed into the basket
● Program Menu: The 'Spray Wash' or 'Agitation Wash' program is selected on the HMI where the RPM and cycle times are set to the operator's specifications.
● Fill: Alcohol is connected from source tank into the centrifuge.
● The Wash cycle: The plant material undergoes an agitated wash with a set number of bi-directional agitations
● System Draining: When the wash cycle is complete, the outlet valve is manually opened and the liquid drained. The alcohol wash is pumped to a properly rated storage reservoir for further processing.
● Spin Dry Cycle: The 'Spin Dry' menu is selected on the HMI and the drying cycle is started. The wet plant solids are spun dry of the remaining alcohol mixture within.
● System Unloading: Upon completion of the 'Dry cycle', centrifuge is unloaded by taking the filter bag out from the basket.
● Repeat Process.
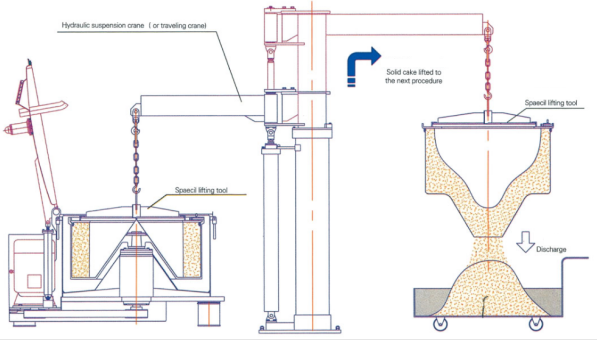