-
WhatsApp
-
Email
Falling film evaporator uses high heat pressure energy to react to materials. It has certain risks in the process of use. The single-effect falling film evaporator has low safety risk, especially the multi-effect falling film evaporator uses multiple steam to increase The pressure in the vapor chamber will have a higher risk factor. So we need to understand the knowledge of falling film evaporator to reduce the harm in using falling film evaporator, and we can understand how to maintain falling film evaporator equipment in daily use.
The multi-effect falling film evaporator produced by ZZKD laboratory equipment manufacturer uses corrosion-resistant and high-strength materials for equipment production, and has undergone multiple inspections to ensure the safety performance of the equipment.
Working principle of falling film evaporator
The heating chamber supplies the liquid with the heat needed for evaporation, which promotes the liquid to boil and vaporize; the evaporation chamber completely separates the gas and liquid phases. The vapor generated in the heating chamber carries a large amount of liquid foam. After reaching a large space of the evaporation chamber, these liquids can be separated from the vapor by the effect of self-condensation or a defoamer. The demister is usually located on top of the evaporation chamber.
The evaporator is to vaporize the compressed and liquefied refrigerant from liquid to gas and absorb heat at the same time. The function is to reduce the temperature of the surrounding medium and play a cooling role.
The material is evenly distributed in the heating tubes of the evaporator through the distribution device. The material flows from top to bottom under the action of gravity and vacuum induction and air flow. During the movement, the material exchanges with the heating steam on the outer wall of the heating tube and evaporates. The main body of the equipment consists of Ⅰ, Ⅱ, and Ⅲ-effect heaters, separators, heat-pressing pumps, condensers, sterilizers, insulation pipes, feed pumps, water pumps, and instrument cabinets.
Advantages of multi-effect falling film evaporator
The characteristics of different effects in the evaporative concentrator, whether in the multi-effect falling film evaporator or in the multi-effect external circulation equipment and extraction and concentration equipment, these different effects have the same feature, which is the efficiency The more you can save more steam and reduce energy consumption.
Falling film evaporator can be divided into single-effect and multi-effect evaporation. If the secondary steam generated by evaporation is directly condensed and no longer used, it is called single-effect evaporation. If the secondary steam is used as the next effect heating steam and multiple evaporators are connected in series, this evaporation process is multi-effect evaporation.
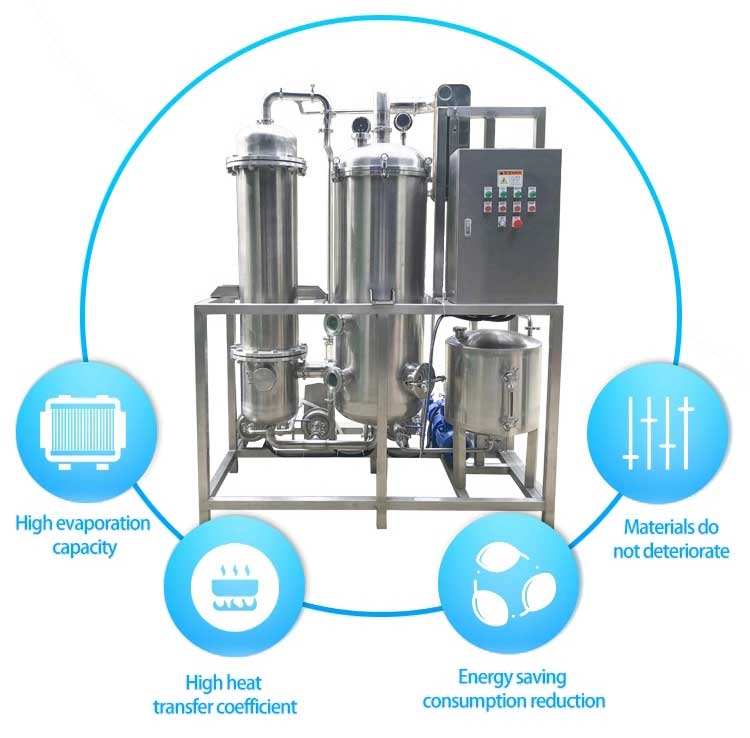
How a falling film evaporator increases the energy of the second vapor
The falling film evaporator uses a compressor to increase the energy of the secondary steam, and utilizes the secondary steam with increased energy to recover the latent heat of the secondary steam. Specifically: the secondary steam generated by the evaporator is compressed by the adiabatic compression of the compressor to increase the pressure and temperature, and then sent to the heating chamber of the evaporator as heating steam to condense and release heat, so the latent heat of the steam is recovered use.
After the secondary steam is compressed by the steam compressor, it is sent to the shell of the falling film heating chamber as heating steam. There is a plate on the shell side of the falling film heating chamber, which guides the secondary steam, condenses and discharges the non-condensable gas. The material to be vaporized enters from the top of the falling film evaporator through the falling film evaporator feed pump and passes through the evaporation tube (tube side). The material is distributed into the heat exchange tube in a film form through the cloth falling film evaporator, and the material flows down the tube by gravity. When the cavity is heated by the steam outside the tube, evaporation occurs when the evaporation temperature is reached, and the material together with the secondary steam flows down from the tube and evaporates in the form of a thin film.
During the flow of the falling film evaporator, it is heated and vaporized by the shell-side heating medium. The generated steam and liquid phase enter the separation chamber of the evaporator. After the vapor and liquid are fully separated, the steam enters the condenser to condense (single effect operation) or enter A one-effect evaporator is used as a heating medium to achieve multi-effect operation, and the liquid phase is discharged from the separation chamber.
The falling film evaporator process can be divided into four types: forward, countercurrent, mixed, and advection
1. Downstream: The solution and steam flow in the same direction, and both flow from the first effect to the last effect. The raw material liquid is pumped into one effect, and automatically flows into the next effect depending on the pressure difference between the effects, and the liquid is pumped out from the last effect (usually operated under negative pressure). Because the pressure of the latter effect is low, the boiling point of the solution is also low. When the solution enters the latter effect, the solution will flash part of the water and generate more secondary steam. Because the concentration of the aftereffect is higher than the previous effect and the operating temperature is lower The heat transfer coefficient of the first effect is often much higher than the last effect. The downstream process is generally suitable for processing heat-sensitive materials at high concentrations.
2. Counter current: The raw materials are sent from the last effect to the pre effect by the pump, the finished liquid is discharged from the first effect, and the material liquid and steam flow in reverse. It is generally suitable to handle solutions whose viscosity changes greatly with temperature and concentration, and it is not easy to handle heat-sensitive materials.
3. Mixed flow: The combination of forward and backward flow has both the advantages of forward and backward flow to avoid its disadvantages, but the operation is complicated and requires a high degree of self-control.
4. Advection: All the effects are fed with the completion solution, and each effect has crystals precipitated, which can be separated in time. It is generally used for the evaporation of saturated solutions.
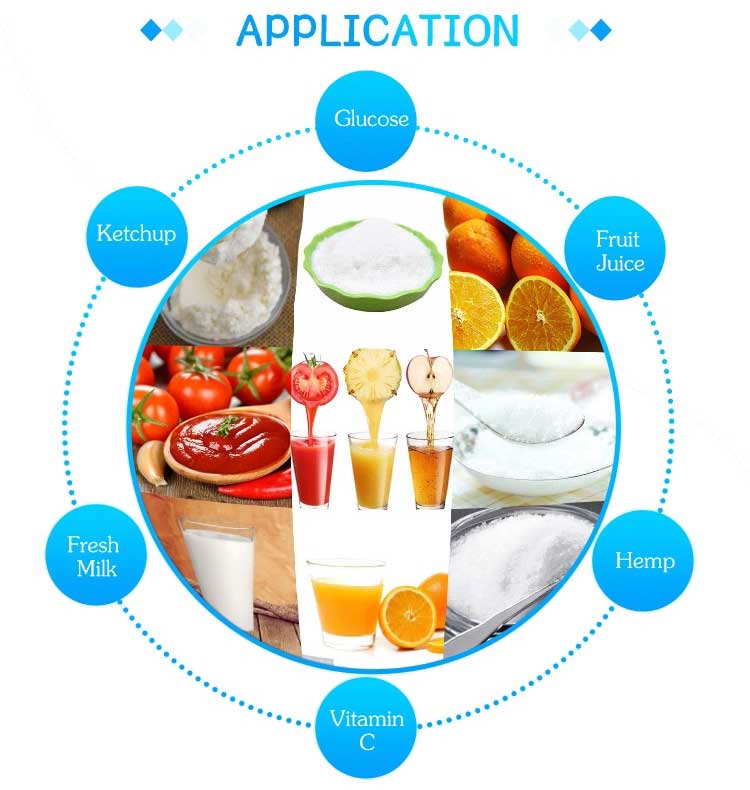
Application of falling film evaporator
Falling film evaporator is used for evaporation and concentration of water or solvent solutions in food, chemical, light industry and other industries, and can be used for waste liquid treatment in the above industries. It is suitable for heat-sensitive materials. The equipment operates continuously under vacuum and low temperature conditions. It has high evaporation capacity, energy saving and consumption reduction, low operating costs, and can guarantee the invariance of materials during evaporation. 1. Large-scale equipment adopts a vertical floor-standing structure. The entire equipment has a compact structure, a small footprint, and a simple and smooth layout. 2. After the vapor and liquid are separated at the bottom of the evaporator, the liquid enters the separator and then separates, which strengthens the separation effect and makes the whole The device has greater operational flexibility. 3. The top of the evaporator sprays or feeds through multiple overflow film distribution devices to ensure that the liquid is evenly distributed in the evaporator film tube, forming a film, greatly improving the heat transfer coefficient, increasing the evaporation rate, and preventing "dry walls" phenomenon. The circulating cooling water of the evaporator contains a large amount of salt substances, corrosion products and various microorganisms. Since the water is not treated, a large amount of calcium magnesium carbonate scale and algae and microorganisms will be formed on the water side after the evaporator is operated for a period of time. Sludge, slime, etc. These dirt are firmly attached to the inner surface of the copper pipe, which leads to deterioration of heat transfer, increased circulation pressure, and reduced unit vacuum, which affects the unit's operating efficiency and causes large economic losses.
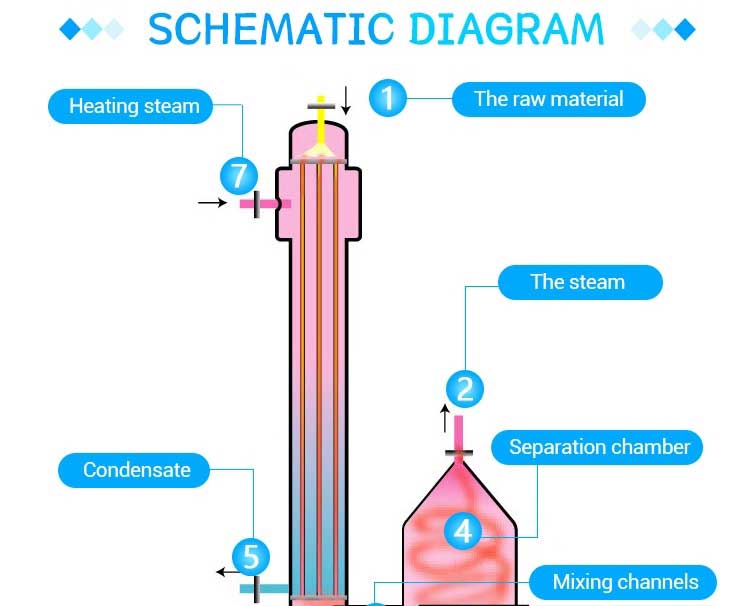
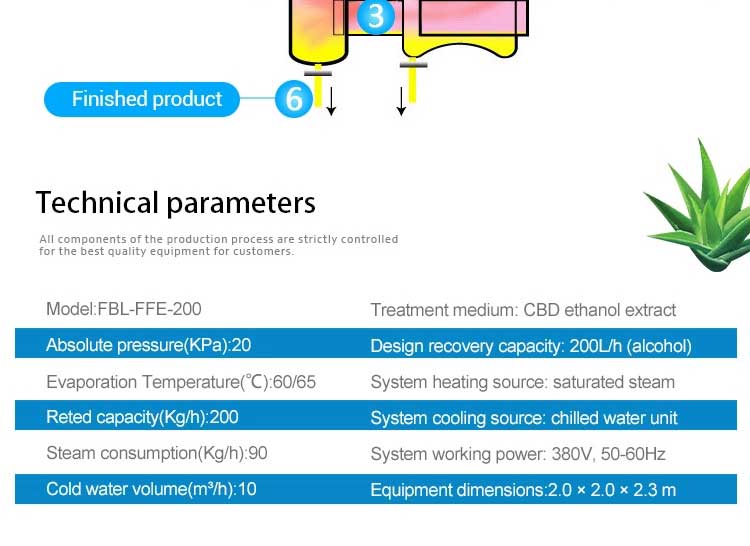
Preventive scaling measures for falling film wastewater evaporator
Falling film evaporator is to add the material liquid from the upper box of the heating chamber of the falling film evaporator, and evenly distribute it into each heat exchange tube through the liquid distribution and film forming device. Under the action of gravity and vacuum induction and air flow, it becomes a uniform film Top-down flow.
The circulating cooling water of the evaporator contains a large amount of salt substances, corrosion products and various microorganisms. Since no water treatment is performed, a large amount of calcium magnesium carbonate scale and algae and microbial sludge will be formed on the water side after the evaporator is operated. Sludge, etc., these dirt extend to the inner surface of the copper pipe, which leads to the deterioration of heat transfer, the increase of the circulation pressure, the reduction of the unit's vacuum, which affects the unit's operating efficiency and causes economic losses.
Preventive scaling measures of falling film wastewater evaporator:
During the process of evaporation and vaporization of concentrated salt wastewater, secondary steam mist is easy to be entrained. The salt water droplets contained in the mist are attached to the screen or baffle of the demister, and the crystals are continuously concentrated to form a scale layer. Sometimes the secondary steam is blocked.
As the concentration of circulating concentrated salt wastewater continues to increase, the calcium sulfate, calcium carbonate, and silicate contained in the wastewater will precipitate in the gaps of the distributor of the falling film evaporator, and fouling will occur, which will cause partial distributor blockage.
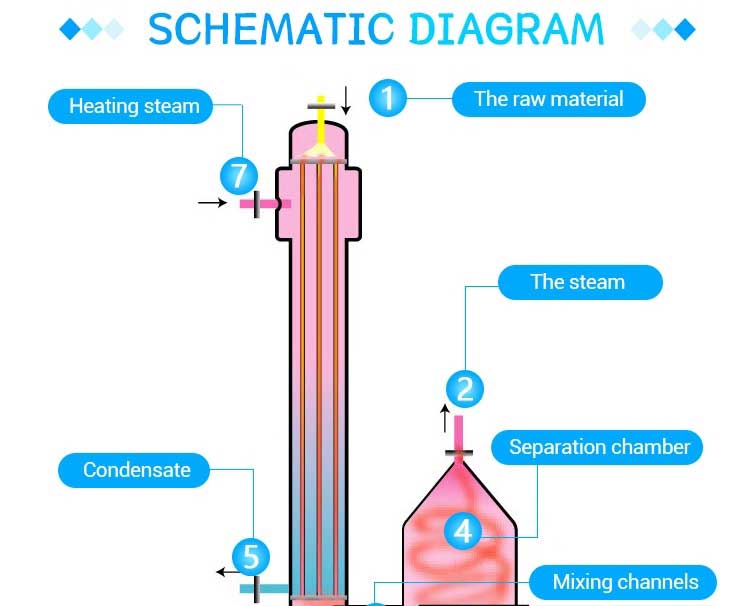
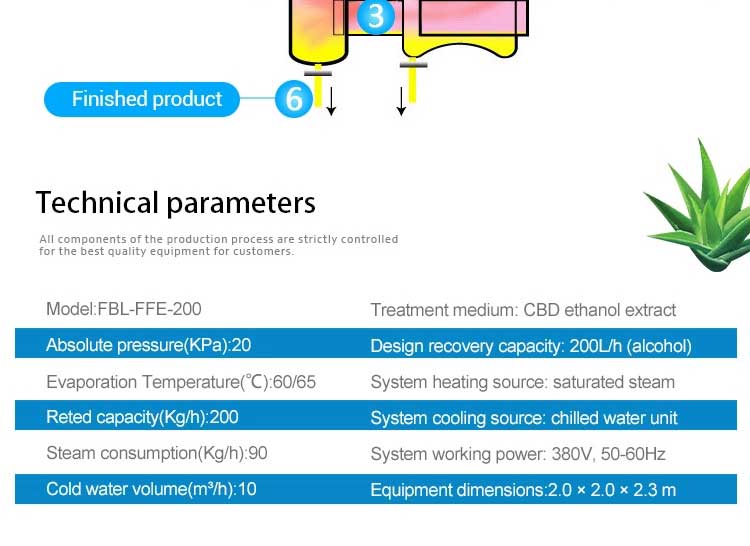
Falling film evaporator forms the circulation mode of the material in the heating pipe and the falling pipe
In a falling film evaporator, the liquid and steam flow downward and co-currently. The concentrated liquid needs to be preheated to the boiling temperature. The uniform liquid film enters the heating tube through the liquid distribution device on the top of the evaporator and flows downward at the boiling temperature. And part of the evaporation, the gravity of the downward movement date is continuously strengthened by the co-current steam flow.
The biggest advantage of the falling film evaporator cooling tube is that the structure is simple, suitable for production, and the dry consumption caused by unpackaged food stored in the warehouse is reduced. However, the heat transfer coefficient of the tube is reduced, and the operation is difficult during defrost, which is not conducive to automation. For the ammonia direct cooling system, seamless steel pipes are welded, and light tubes or coiled finned tubes are used; for Freon systems, coiled or sleeve-type copper tube finned tube sets are mostly used.
The material of the falling film evaporator is heated by the heating tube, the water vaporizes, and the specific gravity of the material and liquid becomes small, while the material in the central falling pipe is not heated to boiling (the specific gravity of the material and liquid penetrates). Due to the severe difference in heat transfer, the circulation of the materials in the heating tube and the downcomer is formed, and the water is evaporated to achieve the purpose of concentration. After the heated steam releases the latent heat, it becomes water and is discharged from the bottom discharge pipe.
Method for completely evaporating refrigerant of falling film evaporator in tube
The lowering of the boiling point of the falling film evaporator material increases the temperature difference with the heat medium; the function of the film scraper is converted into a liquid film thickness in a turbulent state, which reduces the thermal resistance. At the same time, during the process, the materials are inhibited from forming walls and scaling on the heating surface, and accompanied by good heat exchange. Therefore, the overall heat transfer coefficient of the scraper film evaporator is improved.
The main feature of the falling film evaporator is that the refrigerant completely evaporates in the tube, and the excess becomes excess gas, which is conducive to the use of a thermal expansion valve to automatically adjust the supply. The commonly used refrigerants R22, R134a, R407C, R410A, due to evaporation in the refrigerant pipe, as long as the internal flow speed exceeds 4m / s, the lubricant in the pipeline can be easily brought back to the compressor and returned to the oil.
The above is the previous introduction to the working principle and design concept of the falling film evaporator. ZZKD laboratory equipment manufacturers also produce other distillation equipment such as rotary evaporator, molecular distillation, short path distillation kit, etc.
ZZKD laboratory equipment manufacturers are committed to providing customers with efficient and safe equipment.