-
WhatsApp
-
Email
Detergent spray dryer overview:
Spray drying is a drying process in which the raw material liquid is put into the atomizer and separated into droplets, and the powder-shaped products are obtained by direct contact of hot air or other gas with the droplets. In the 1930s and 1940s, spray drying technology has been widely used in the production process of detergents, dairy products, dehydrated foods, dyes, cement, and fertilizers. Currently, common milk powder, instant coffee, instant food soup, etc. are the products obtained from the spray drying process. At first, a detergent powder dryer machine was used in my country's dairy industry, and later in the pharmaceutical, dye and detergent industries, and now spray drying technology is widely used in my country. Especially in the pharmaceutical and ceramic industries, spray drying is widely used. Spray drying technology has a special purpose in the pharmaceutical industry. It simplifies and shortens the process and time from Chinese medicine extract to semi-finished or finished products of preparations, and improves production efficiency and drug quality.
The spray drying tower is drying equipment for biological pesticides, medicines and food microorganisms. detergent powder dryer machine is a drying process in which the raw material liquid is put into the atomizer and separated into droplets, and the powder-shaped products are obtained by direct contact of hot air or other gas with the droplets.
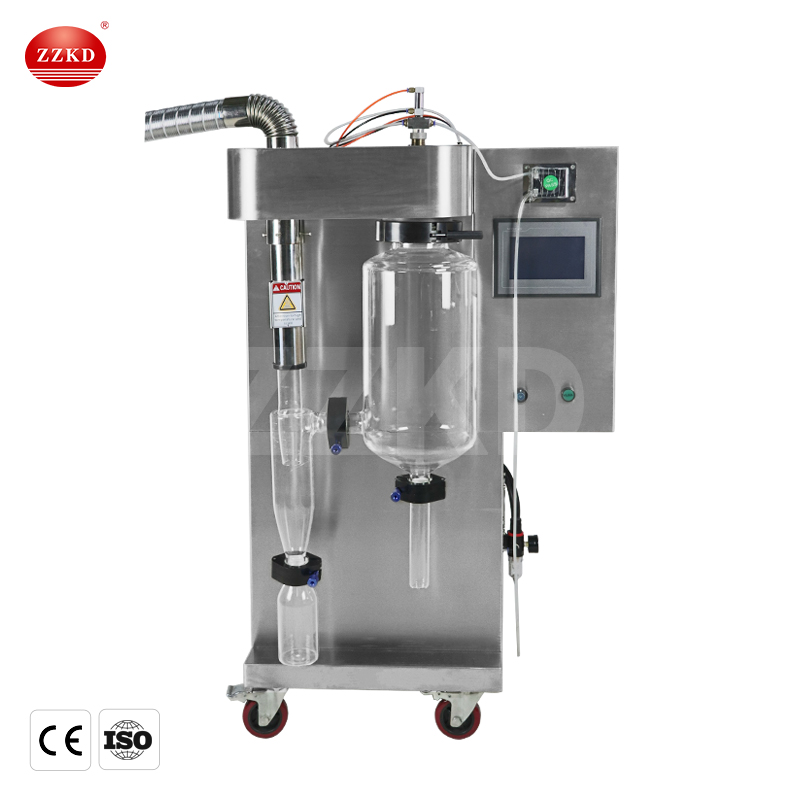
Detergent spray dryer features:
1. The drying speed is fast, and it takes a few seconds to complete;
2. Suitable for drying heat-sensitive materials;
3. Wide range of use: According to the characteristics of the material, it can be used for hot air drying, centrifugal granulation and cold air granulation, and most products with large differences in characteristics can be produced by this machine;
4. Since the drying process is completed in an instant, the particles of the finished product can basically keep the spherical shape of droplets, and the product has good dispersibility, fluidity and solubility;
5. The production process is simplified and the operation control is convenient. Spray drying is usually used for solutions with a solid content of less than 60%. After drying, there is no need for pulverization and screening, which reduces the production process and simplifies the production process. The particle size, bulk density and water content of the product can be adjusted by changing the operating conditions within a certain range, and the control and management are very convenient;
6. In order to prevent the material from being polluted and prolong the life of the equipment, all parts in contact with the material can be made of stainless steel.
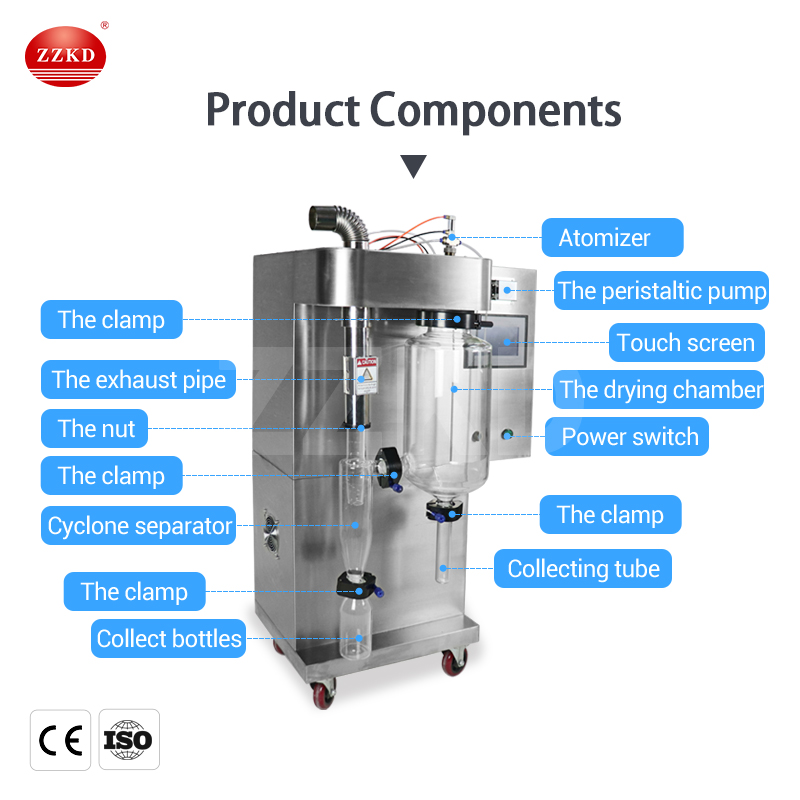
Detergent spray dryer explosion-proof settings;
10l spray dryer cause of the explosion:
The main reasons for dust combustion or even explosion are that the dust moisture content is too low, the dust is too fine, the inlet air temperature is too high, and the continuous production time is too long during the production process of spray drying. It may burn or even explode when it encounters static electricity or friction. Secondly, combustion explosion is also directly related to the nature of dust.
Detergent spray dryer production notes:
Most of the spray drying production is continuous production, that is, 24 hours without stopping. Dust combustion and even explosion often occur at night. People do not track production parameters in time, resulting in a period of negligence. Therefore, the 10l spray dryer parameters in the production process should be strictly monitored in real-time, and some production parameters should be tracked and recorded in real-time. When the parameters fluctuate, especially when the moisture content of the dust is low, it should be adjusted in time, otherwise, the dust may burn or even explode. Danger. Secondly, measures should be taken to shield the sparks that may cause static electricity. Some dust has secondary drying in the drying process, such as fluidized bed secondary drying. The fluidized bed is prone to static sparks, which must be avoided in the production.
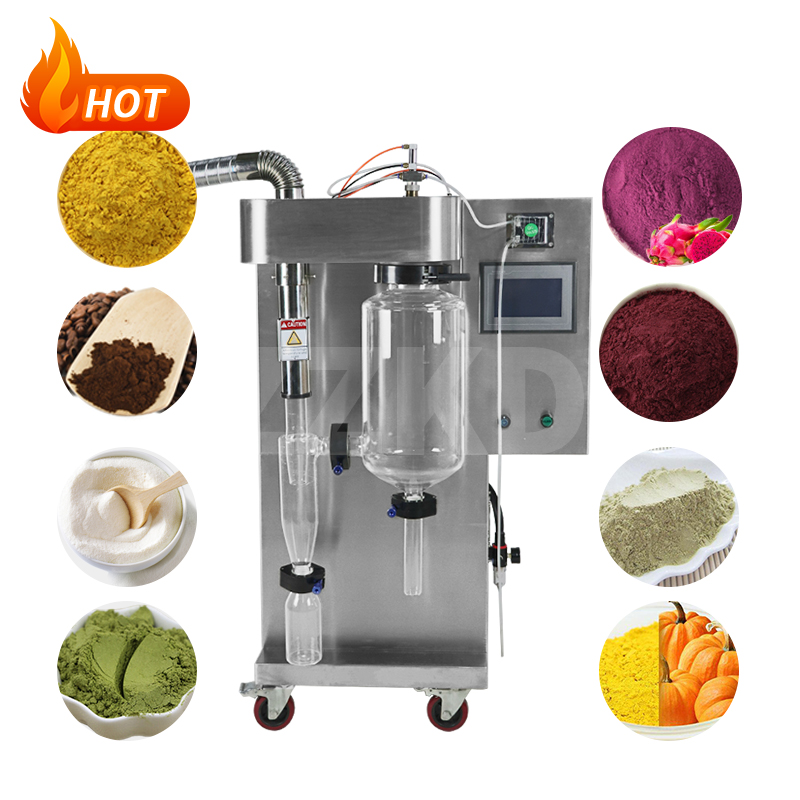
Detergent spray dryer operation precautions:
1. the First turn on the centrifugal fan, then turn on the heater, and check whether there is air leakage. If it is normal, it can be preheated. Because the hot air preheating determines the evaporation capacity of the drying equipment, without affecting the quality of the material to be dried, should be Increased the inlet air temperature as much as possible.
2. During preheating, the top of the 10l spray dryer chamber is placed at the atomizer, and the drying chamber and the cyclone separator must be sealed to prevent cold air from entering the drying chamber and reducing the preheating efficiency.
3. When the inlet temperature of the detergent powder dryer machine chamber reaches the set temperature, turn on the centrifugal nozzle. When the nozzle reaches a high speed, turn on the feed pump, add clean water and spray for 10 minutes and then replace it with the material liquid. The feeding amount should be from small to large. Otherwise, sticking will occur until the appropriate requirements are adjusted. The concentration of the feed liquid should be prepared according to the drying properties of the material to ensure that the finished product has good fluidity after drying.
4. The temperature and humidity of the dried product depend on the exhaust air temperature. It is important to keep the exhaust air temperature constant during operation, which depends on the size of the feeding amount, the feeding amount is stable, and the outlet temperature is relatively stable of. If the solid content and flow rate of the feed liquid change, the outlet temperature will also change.
5. If the temperature of the product is too high, the feeding amount can be reduced to increase the outlet temperature; if the temperature of the product is too low, vice versa. For heat-sensitive materials with lower product temperatures, the feeding amount can be increased to reduce the exhaust air temperature, but the temperature of the product will increase accordingly.
6. Collection of finished products after 10l spray dryer. The pollinator at the lower part of the cyclone, it should be replaced before it is full. When replacing the pollinator, the butterfly valve above must be closed first.
7. If the dried product is hygroscopic, the cyclone separator, its pipeline, and the part of the pollinator should be wrapped with thermal insulation material, so as to avoid the moisture absorption of the dried product.