-
WhatsApp
-
Email
Jacketed glass reactor technology is ideal for mixing, reaction, and distillation in the chemical and pharmaceutical industries. Glass reactors and process equipment ensure optimum efficiency in laboratories, pilot plants/kg labs, and production. Double-walled glass reactor technology is designed by experts to provide users with a first-class jacketed reactor product. We have extensive expertise in scientific glass manufacturing and providing solutions for various chemical processing industries. Borosilicate 100l jacketed glass reactor has the special advantage of response visibility, which is not possible in different building supplies. However, the traditional strategy of heating glass reactor contents forces customers to compromise on visibility advantages. It is the best pilot and production equipment for the synthesis of contemporary fine chemicals, biopharmaceuticals, and the latest consumables. 100L glass reactor vessel, specially manufactured for 100L jacketed glass reactors. There are a total of 6 ports on the reaction hood for the motor, condenser, temperature sensor, solids addition, air release, and funnel plot. High borosilicate glass material, double-layer stirring anchor, corrosion-resistant PTFE material
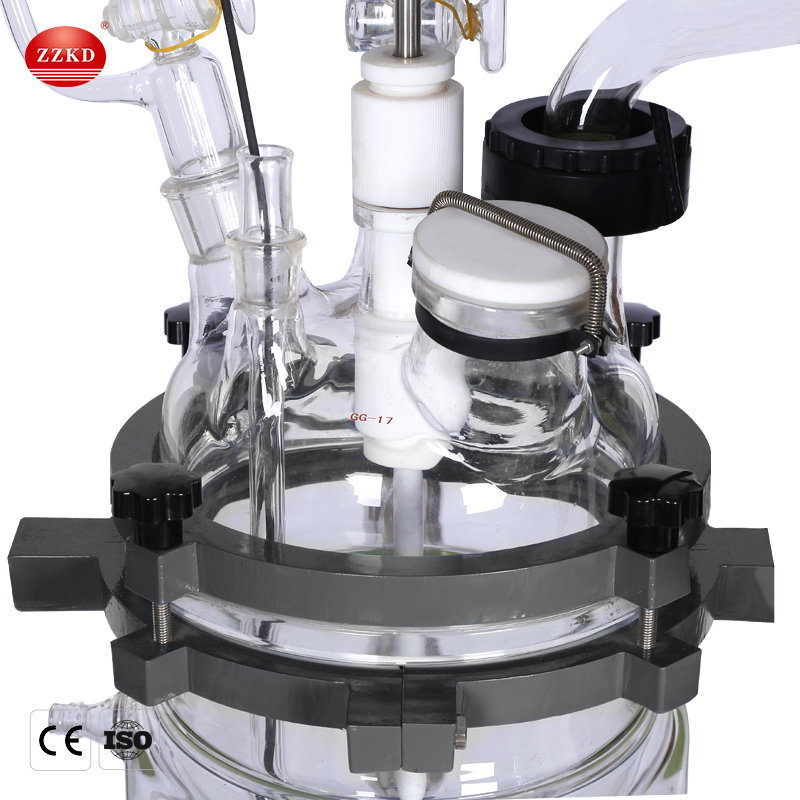
Main uses of glass reactor:
Glass reactors are mainly used for synthesis reaction, distillation, and focusing of various materials. We have a single, double, and triple 100l jacketed glass reactor. Depending on some experimental needs, the reactor can be pumped to an unfavorable strain state. A constant stress funnel or regulating valve on the feeding bottle allows you to add material to the container at an even and controlled rate. Single/double-walled glass reactors are designed for artificial reactions of different types of supplies under controlled temperature and vacuum settings. Each reactor features adjustable stirring speed and a continuous pressure feed funnel, allowing you to add materials to the vessel at a uniform and controlled rate. The built-in condenser makes it possible to recover some materials at a controlled rate. There are two types of quick flange clamps, threaded and straight, which can be connected to completely different devices. 10L receiving bottle, GG-17 borosilicate glass. Jacketed reaction vessels are used to artificially react various materials under controlled temperature and vacuum settings. The reaction vessel can also function under a vacuum, making it ideal for any atmosphere-sensitive application.
Jacketed reactors are ideal for reaction functions involving excessive temperatures. The working temperature is 200℃, max. The temperature difference between the inside and outside of the reactor was 80°C. When heating or cooling the reactor, it is recommended to continuously monitor the temperature inside and outside the vessel, and steadily increase or decrease the temperature to avoid accidents. They include inner jackets for cooling or heating and outer jackets for vacuum insulation. The outer sheath also reduces moisture build-up, so you can always see exactly what's going on inside the system. Crescent moon + three-impeller double-layer stirring paddle, 304 stainless steel + PTFE stirring blade; the stirring rod is made of 304 chrome steel and wrapped with a PTFE tube. Filtration reactors are used to perform single- or multi-step reactions and filtration in the same vessel, they also eliminate material transfer and reduce losses. When heating or cooling the reactor, it is recommended to continuously observe the temperature inside and outside the vessel, and gradually increase or decrease the temperature to avoid accidents. Robust stainless steel reinforced PTFE stirrer with anchored stirrer for a wide range of viscous materials. All glassware is handcrafted from food-grade borosilicate glass, which is heat/cold/corrosion-resistant. Other notable efficiency components are the wide temperature range, excessive thermal shock resistance, and vessel geometry, like industrial vessels. Superior reactivity is provided by a unique annular baffle located within the reactor thermal jacket.
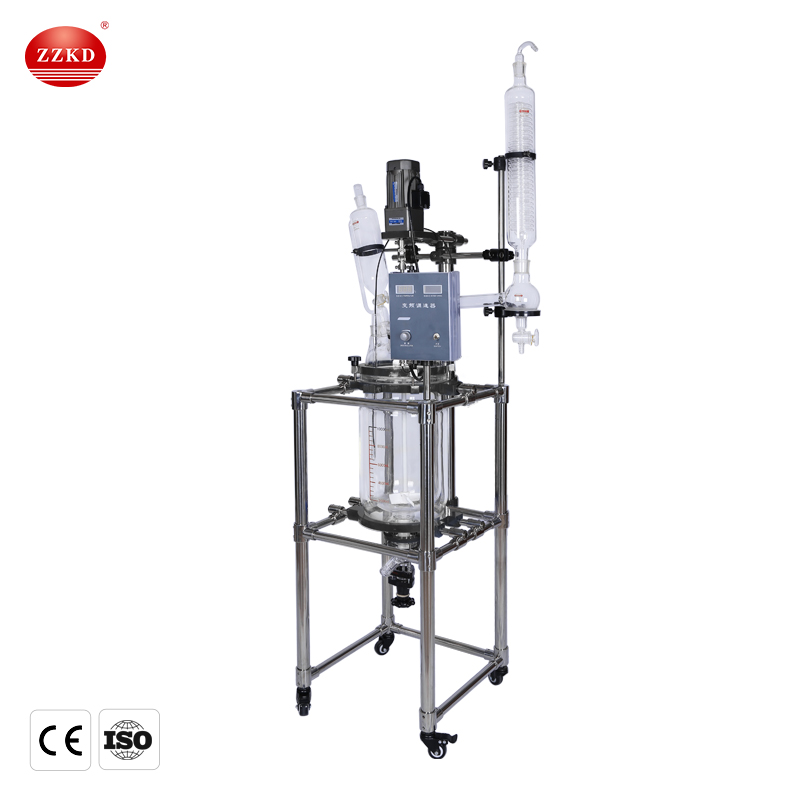
The composition of the glass reactor:
The down drain in the center of the 100l jacketed glass reactor has a sloping drain for direct material discharge. The parts in contact with the materials are all made of high borosilicate glass (expansion coefficient 3.3) and PTFE materials, which have stable performance and are usually not easy to react with materials. Our hazardous area-rated reactors use only high-quality UL-approved components. All components have a visual UL and hazard class marking. This response vessel is rated for safe operation under full vacuum. Please contact us if any additional details are required. The reaction vessel can withstand strains ranging from -0.1MPa to 0MPa. Plug or drain valve in PTFE and FV rubber materials; seal with PTFE covered O-rings. The container can withstand pressures from -0.1MPa to 0MPa. Widely used in prescription drugs, chemicals, biopharmaceuticals, new materials, precious metals, and other fields. PTFE is resistant to most solvents and chemicals.
Speed controller, adjustable speed, and display temperature. Oil vacuum gauge, shockproof when stirring; high environmental protection type condenser. Discharge valve, direct discharge of material.
Plug or drain valve in PTFE and FV rubber materials; seal with PTFE covered O-rings. The temperature of PT100 is displayed by liquid crystal. More accurate temperature measurement and extra convenience.
There are ordinary wheels with brakes at the rear of the gears, which can be moved as a whole and are easy to operate. After the reaction is completed, the fabric can be discharged from the side outlet on the backside of the kettle.
Alloy steel mechanical seals, PTFE joints, handle excessively precise seals under working conditions.
PTFE stirring paddle is suitable for stirring and mixing low-viscosity or high-viscosity liquids. It also provides excellent mixing in laboratory reactors at atmospheric or sub-atmospheric strain.
The container can withstand the pressure range of -0.1MPa to 0MPa.
Solvent-resistant Teflon seal ensures very long durability and operation with a seal of 0.098Mpa. Wide operating temperature range from -60°C to 250°C.
High borosilicate glass has good physical and chemical properties
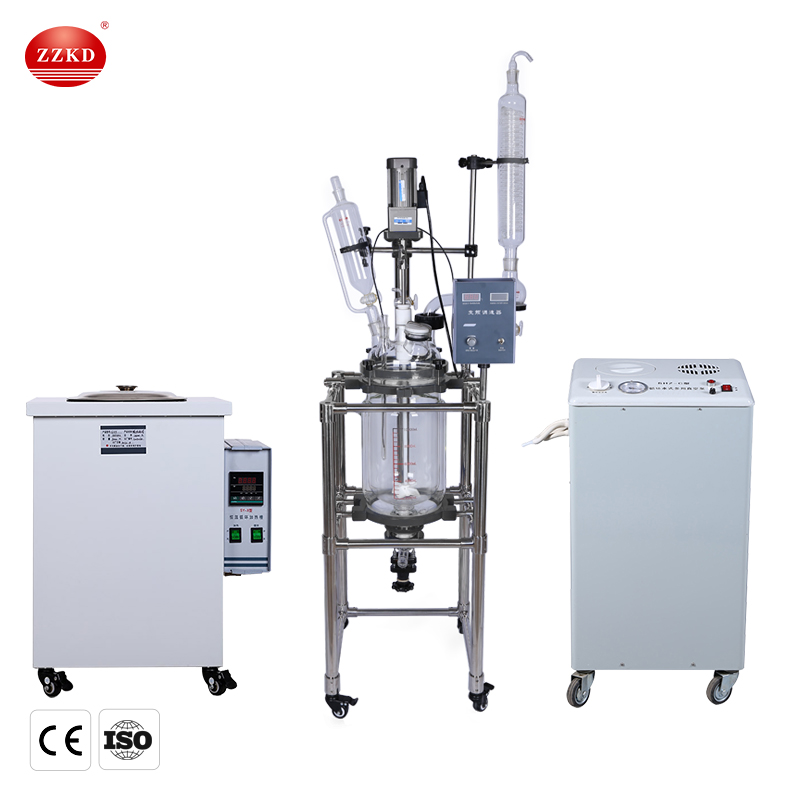
The advantages of glass reactor:
Jacketed glass reactors are designed for synthetic reactions of a variety of materials in a controlled temperature and vacuum environment. Double-walled glass reactors are designed to react and mix different types of materials under specific adjustable temperature and vacuum conditions. The lid is fully customizable to the buyer's needs. The company keeps pace with the times and can present reactor systems ranging from simple to complex processes. We will continue to pursue the dedication of "integrity and innovation" and provide customers with excellent pre-sale, in-sale, and after-sale services. If you are interested in wholesale, please contact us as these items are not listed on the website but can be purchased by phone or email.