-
WhatsApp
-
Email
The best closed loop extraction system is characterized by the separation of air from the solvent during the extraction process, which is the main difference between it and the open-loop extraction method. The system consists of several specialized units, such as a solvent storage tank, a recovery tank and several pumps. The solvent of this system can be recycled. It minimizes the risk of explosion and provides a safe method of working with flammable solvents.
There are many types of closed loop extraction kit, and there are more than 30 different extraction equipment currently used in industrial production. Typical extraction equipment includes mixer-settler tanks, extraction columns and centrifugal separators. Although solvent extraction plays an important role in many industrial separation fields, traditional solvent extraction technology and solvent extraction equipment still have their own shortcomings. Therefore, in recent years, with the rapid development of other separation technologies, many researchers have been studying new solvent extraction technologies and improving solvent extraction devices to meet the needs of new industrial production. This paper mainly introduces two aspects: high capacity closed loop butane extractor and best closed loop extraction system.
There are many types of closed loop extraction kit, and there are more than 30 different extraction equipment currently used in industrial production. Typical extraction equipment includes mixer-settler tanks, extraction columns and centrifugal separators. Although solvent extraction plays an important role in many industrial separation fields, traditional solvent extraction technology and solvent extraction equipment still have their own shortcomings. Therefore, in recent years, with the rapid development of other separation technologies, many researchers have been studying new solvent extraction technologies and improving solvent extraction devices to meet the needs of new industrial production. This paper mainly introduces two aspects: high capacity closed loop butane extractor and best closed loop extraction system.
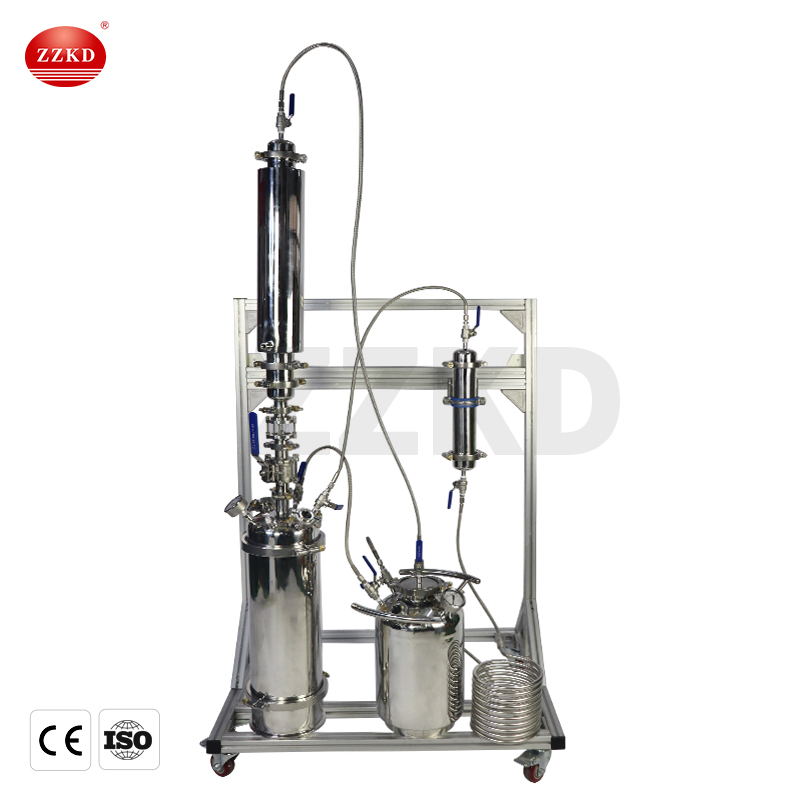
High capacity closed loop butane extractor:
Butane is a colorless gas with a slightly unpleasant odor. Its properties are insoluble in water, soluble in alcohol and chloroform, flammable and explosive. It is also used to a certain extent in modern production and life, Subcritical biotechnological extraction of solvents up, refrigerants and organic synthesis raw materials, as small as cooking and industrial heating are the application fields it involves. So today, let's talk about the preparation process and application range of butane
Preparation process of butane:
Oilfield gas, wet natural gas and cracked gas all contain n-butane, which is obtained by separation.
(1) Separating oilfield gas and wet natural gas by pressurizing and condensing them to obtain liquefied petroleum gas containing propane and butane, and then separating butane by distillation.
(2) Separation of the C4 fraction from petroleum cracking and the gas obtained by vacuum distillation at room temperature in the refinery, through reforming, catalytic cracking, coking, thermal cracking, hydrocracking, the liquid gas obtained can obtain a large amount of C4 fraction, by reforming, The C4 fraction obtained by hydrocracking and atmospheric and vacuum distillation is mainly butane (n-butane and isobutane). The C4 fraction produced by the ethylene unit also contains butane. For example, the yield of butane in the medium-depth cracking product of naphtha is 0.19% (weight ratio), accounting for 6.5% of the C4 fraction. The tail gas from the catalytic cracking unit is fractionated to separate the C3 fraction, isobutene and C5 fraction, and then sent to the front acetonitrile extractive distillation tower from the bottom of the tower, and more than 90% of n-butane is obtained from the top of the tower.
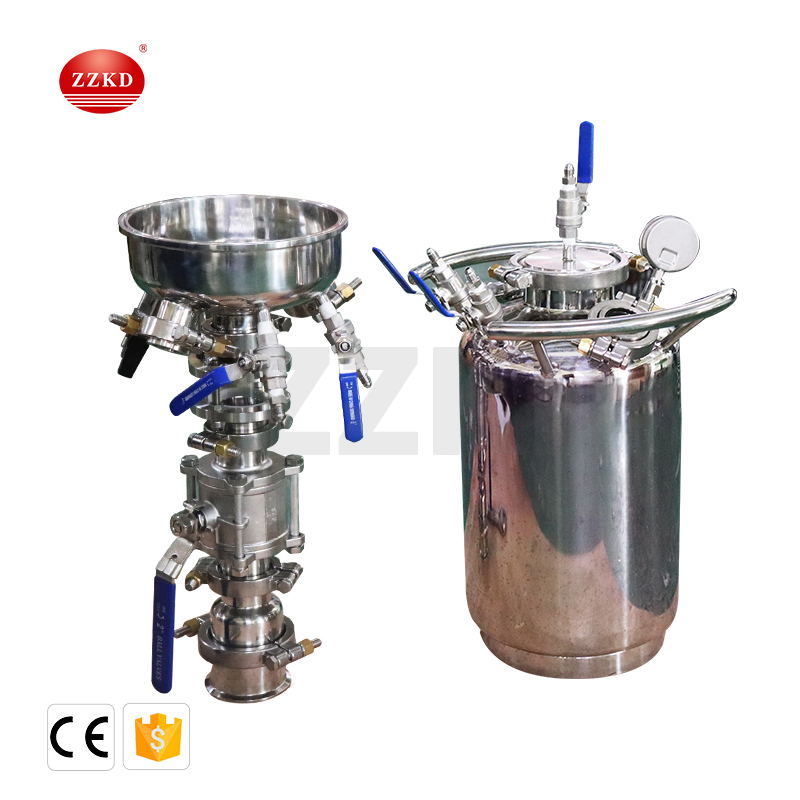
The scope of application of butane:
In addition to being directly used as fuel, n-butane is also used as a subcritical biotechnology extraction solvent, refrigerant and organic synthesis raw material. Butane is dehydrogenated in the presence of a catalyst to form butene or butadiene, isomerized to isobutane in the presence of sulfuric acid or anhydrous hydrofluoric acid, Isobutane is catalytically dehydrogenated to form isobutene, and isobutane can be used as an alkylating agent Reacts with olefins to form branched chain hydrocarbons with good antiknock performance. Catalytic oxidation of butane can produce maleic anhydride, acetic acid, acetaldehyde, etc.; halogenation can produce halobutane; nitration can produce nitrobutane; catalysis at high temperature can produce carbon disulfide; steam reformation Hydrogen can be produced. In addition, butane can also be used as a motor fuel blend to control volatile components; it can also be used as a deasphalting agent for heavy oil refining; a wax precipitation agent in oil wells; an overflow agent for secondary oil recovery, resin foaming agent, and seawater conversion Refrigerant for fresh water, and olefinic agent Göhler polymerization solvent, etc.
What is extraction technology:
The extraction system is an analytical instrument used in the fields of chemistry, biology, chemical engineering, and food science and technology. transfer from one solvent to another. After repeated extractions, most of the compounds were extracted. The solvent extraction process generally consists of extraction, washing and back extraction.
The characteristics of the extraction method:
① The operation can be continuous, the extraction speed is fast, the production time is short, and the energy consumption is low;
② Less damage to heat-sensitive substances;
③Multi-stage extraction can be used;
④The consumption of solvent is large.
Solvent selection principle:
① The larger the partition coefficient, the better, and the solvent with similar structure to the substance to be separated is used;
②Select a solvent with a separation factor greater than 1;
③ It is better that the mutual solubility of the feed liquid and the extraction solvent is low;
④Choose a solvent with low toxicity.
The composition of the optimal closed loop extraction kit:
The best closed-loop extraction system mainly consists of ten parts, namely: Cap with shower head, Dewaxed column, filter plate, Ball valve, Collection chamber, Splatter platter, PTFE lined stainless steel hose, Dryer
recovery tank with flat bottom, Cold trap
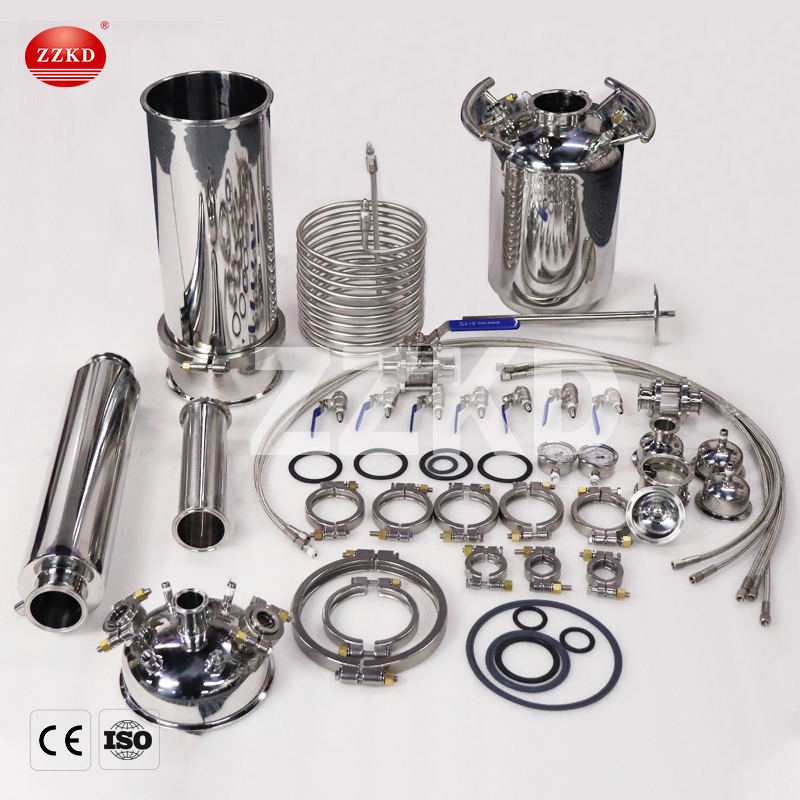
How to choose the closed loop extraction kit?
The selection and design of equipment mainly depends on the materials to be processed and the inherent characteristics of the equipment. Various types of extraction equipment have different characteristics, and the properties of the material in the extraction process have a complicated impact on the operation. For the specific extraction process, the principle of selecting suitable equipment is: first meet the process conditions and requirements, and then consider closed loop extractor price. Equipment fees and operating fees tend to be minimal. The selection of extraction equipment should consider the following factors.
① The theoretical level required
When the required theoretical stages are not more than 2 to 3 stages, all kinds of extraction equipment can meet the requirements; when the required theoretical stages are more (such as more than 4 to 5 stages), sieve tray towers can be used; when When the number of theoretical stages required is more (such as 10 to 20 stages), equipment with additional energy, such as pulse towers, turntable towers, reciprocating sieve tray towers, mixing-clarifying tanks, etc, can be selected.
②Production capacity
When the processing capacity is small, packed towers and pulse packed towers can be selected. For larger production capacity, sieve tray towers, turntable towers, and mixing-clarifier tanks can be used. The processing capacity of centrifugal closed loop extraction kit is also quite large.
③Physical properties of matter system
For systems with small interfacial tension and large density difference, equipment without external energy can be used. On the contrary, if the interfacial tension is large and the density difference is small, the equipment with external energy should be selected. For difficult-to-layer systems with very small density difference, large interfacial tension and easy emulsification, centrifugal closed loop extractor price should be used.
④For highly corrosive systems, packing towers and pulse packing towers with simple structures should be used. For the extraction of radioactive elements, pulse towers and mixing-settling tanks are used more.If there are suspended solids in the system or precipitates are generated during operation, periodic shutdowns are required for cleaning. Generally, a rotary disk extraction tower or a mixing-settling tank can be used. In addition, the reciprocating sieve tray column and the liquid pulsating sieve tray column have a certain self-cleaning ability, and can also be considered for use in some occasions.