-
WhatsApp
-
Email
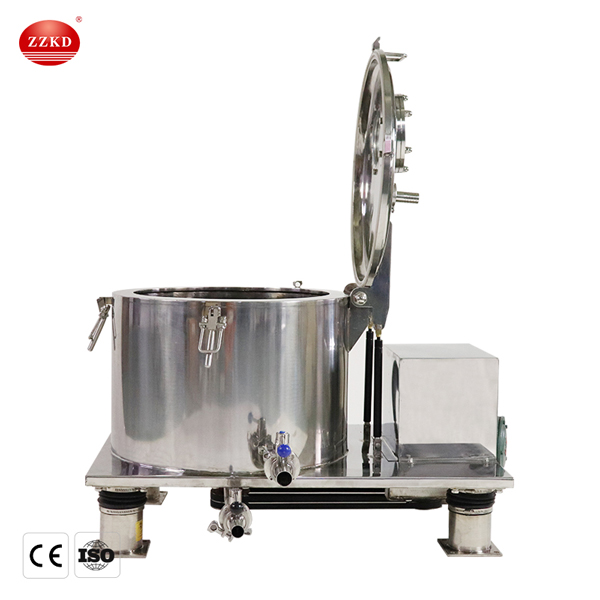
Working principle of bottom discharge centrifuge machine:
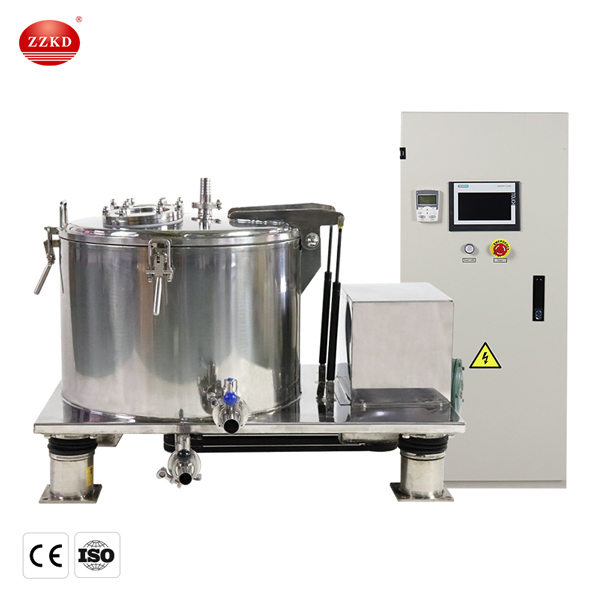
Performance advantages of bottom discharge centrifuge machine:
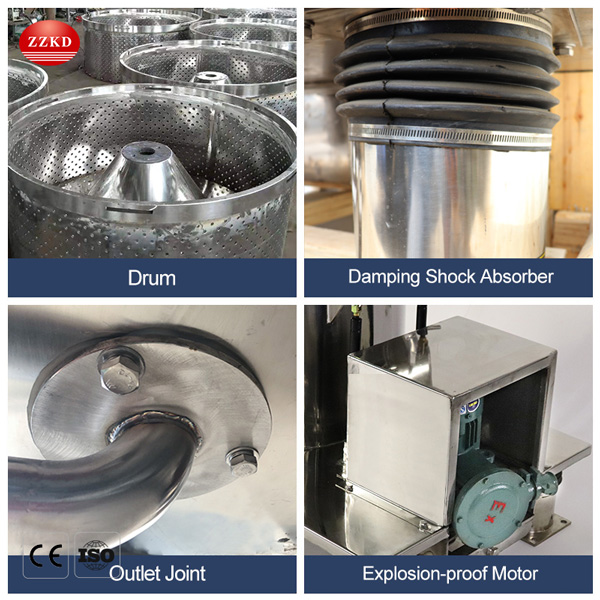
Compared with other separation machines, bottom discharge centrifuge machine can not only obtain solid phase with low moisture content and high-purity liquid phase, but also have the advantages of small size, good sealing, continuous operation, automatic so remote etc. control, They are widely used in chemical industry, Petrochemical, petroleum refining, light industry, medicine, food, textile, metallurgy, coal, mineral processing, shipbuilding, environmental protection, military and other departments, such as coal powder recovery for wet coal dral mud purification and reuse for oil mining; shaft Concentration of isotopes; sludge concentration and dehydration of sewage treatment; refining of petrochemical products; extraction of antibiotics and pesticides; manufacture of milk, yeast, beer, fruit juice, sugar, orange oil, animal vegetable oil, rice bran oil, starch and other foods; the dehydration of fabric fibers; the purification of lubricating oil and fuel oil all re require the use of centrifuges. Decanter centrifuge supplier can be seen that centrifuges have become widely used separation equipment in various sectors of the national economy.
Model | PPTD-10 | PPTD-30 | PPTD-50 | PPTD-135 | PPTD-200 | PPTD-400 | PPTD-500 |
Drum capacity (L) | 14 | 40 | 85 | 185 | 295 | 450 | 510 |
Jacket volume (L) | 22 | 30 | 43 | 75 | 110 | 150 | 155 |
Loading limit (lbs) | 15 | 60 | 120 | 270 | 500 | 940 | 1060 |
Plant material loading limit (lbs) | 4 | 16 | 30 | 70 | 100 | 180 | 240 |
Speed (R/ min) | 2700 | 1900 | 1500 | 1200 | 1000 | 960 | 960 |
Separation factor (g) | 1225 | 910 | 755 | 645 | 560 | 620 | 645 |
Motor (kW) | 1.1 | 1.5 | 3 | 5.5 | 7.5 | 15 | 18.5 |
Frequency converter (kW) | 1.5 | 2.2 | 4 | 7.5 | 11 | 18.5 | 22 |
Net weight (kg) | 280 | 400 | 750 | 1700 | 2350 | 3100 | 3350 |
Drum diameter (mm) | 300 | 450 | 600 | 800 | 1000 | 1200 | 1250 |
1 Buisness Type
--Factory located in Zhengzhou, Henan, CN
-- Factory covers an area of 2000m2
-- Employees,over 60 people
2 What are your mian products?
--Single layer glass reactor
-- Jacketed Glass Reactor
-- Vacuum Rotary Evaporator
-- Vacuum Drying Oven
-- Blast Drying Oven
-- Other simple Lab facilities
3 How to make order
--communicate with our salesman
--items would be PDF/JPF/Vidio format offer free design service for all clients
-- order to us after samples approved
-- all workmaters try best to produce sample
--arrange shippment when your balance arrives
--supply related acceossries
--welcome your second order and further more orders in future
4 Quanlity asssurance
--Every board has been checked at least 4 times
--100% inspection before shppment